项目概述
本项目旨在实现CNC加工过程中原料的自动上下料,以及必要的检测与清洗流程。通过引入复合AGV(自动导引车)机械手系统,结合扫码相机与定位视觉相机,实现精准、高效的物料搬运与流程管理。
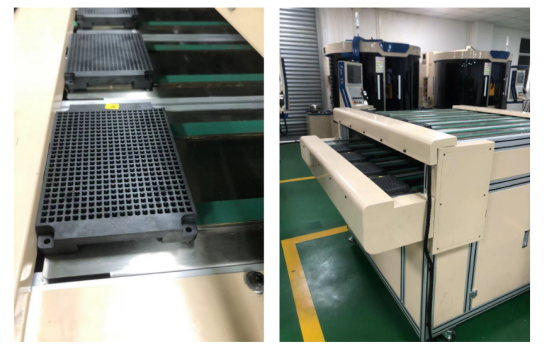
系统组成
1、复合AGV机械手系统:包含AGV车体、机械手臂、扫码相机、定位视觉相机等关键组件。
2、控制系统:负责接收②区域设备系统发出的任务信号,控制AGV机械手系统完成物料的抓取、搬运、放置等动作。
3、扫码系统:通过扫码相机读取物料盘上的二维码,实现物料信息的录入与跟踪。
4、定位系统:利用定位视觉相机实现AGV机械手系统的精准定位与导航。
工作流程

1、原料抓取:复合AGV机械手系统根据控制系统指令,前往原料立库第一层抓取待加工物料。
2、加工工序:将抓取到的物料送达②区域机台,按照机台内部的放料位进行放置,并等待加工。
3、检测工序(可选):若系统发出检测需求,将②区域机台检测位的模具盘送至③号检测设备放置区进行检测。检测完成后,再将模具盘送回②区域机台。
4、清洗工序:将②区域设备加工好的物料放置在④区域清洗机输送线上,由输送线自动完成物料的清洗工作。
技术实现
1、复合AGV机械手系统:采用先进的AGV技术与机械手臂技术,实现高效、精准的物料搬运。
2、扫码系统:采用高性能扫码相机,确保物料信息的准确录入与跟踪。
3、定位系统:利用先进的视觉定位技术,实现AGV机械手系统的精准定位与导航。
4、控制系统:采用可靠的控制系统,确保整个系统的稳定运行与高效协作。
系统优势
1、自动化程度高:实现CNC加工过程中原料的自动上下料、检测与清洗,提高生产效率。
2、精准度高:通过扫码相机与定位视觉相机,实现物料信息的准确录入与精准定位。
3、灵活性强:可根据实际需求灵活调整工作流程,满足不同的生产需求。
4、可追溯性强:通过扫码系统实现物料信息的全程跟踪与追溯,提高产品质量管理水平。