在工业4.0与智能制造高速发展的今天,具身智能工业机器人已从单一执行设备演变为多任务协同的智能体。然而,复杂动态环境中的路径规划问题——如动态避障、多机协同、高精度定位等——仍是制约效率提升的核心痛点。传统单一算法常面临适应性差、计算成本高或实时性不足的局限,而复合机器人路径规划算法通过多技术融合与分层优化,正成为具身智能工业机器人突破瓶颈的关键钥匙,推动工业自动化迈向更高阶的“智”变。
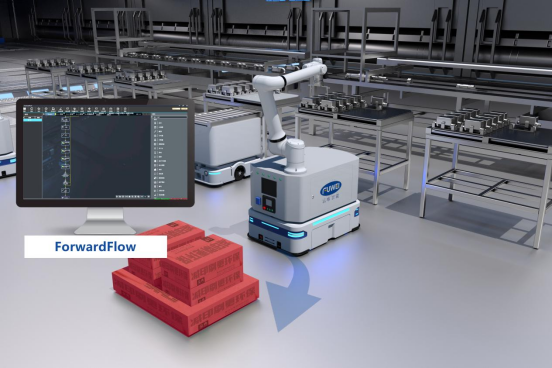
一、复合算法:具身智能机器人的“决策大脑”
复合机器人路径规划算法的核心在于整合多种技术优势,为具身智能工业机器人构建“感知-决策-执行”的全链路闭环。例如:
1.仿生优化与深度学习结合:借鉴蜻蜓优化算法(DA)的群体智能搜索能力,结合深度强化学习(DRL)的动态策略优化,使机器人可在复杂栅格地图中快速生成全局最优路径,并实时调整局部避障策略,充分释放具身智能工业机器人的自主性。
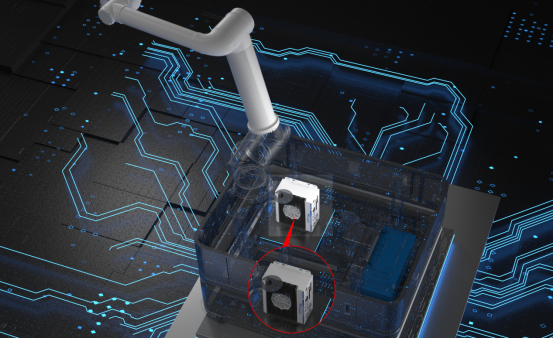
2.多传感器融合与动态建模:集成激光雷达、视觉相机与力觉反馈,构建高精度环境模型,使算法能适应光照变化、障碍物移动等动态干扰,显著提升具身智能工业机器人的鲁棒性。
3.这种多模态融合的复合机器人路径规划算法,不仅解决了传统算法在复杂场景中的“水土不服”,更通过模块化设计实现快速部署,为具身智能工业机器人在工业现场的多样化需求提供技术底座。
二、场景赋能:从智能仓储到高危作业
1.智能仓储物流
在仓储环境中,复合算法可协调AGV、机械臂与无人叉车协同作业。例如,基于协作搜索优化(CSO)的路径规划,具身智能工业机器人实现多机动态避障与任务分配,物流效率提升40%以上。静电放电优化(EDO)算法通过模拟电荷斥力,在密集货架中规划安全路径,避免碰撞风险。
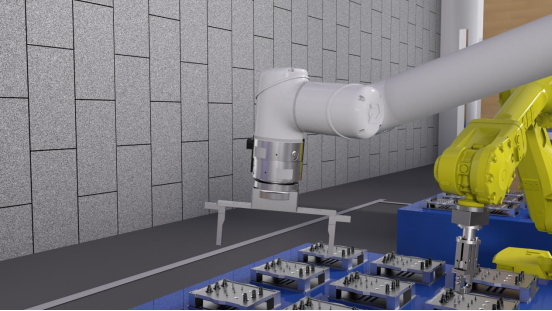
2.柔性制造产线
针对多品种、小批量生产需求,算法结合遗传算法(GA)的全局搜索与粒子群优化(PSO)的快速收敛特性,使具身智能工业机器人实现混线物料的高效分拣与装配。例如,汽车零部件装配中,路径规划精度达±0.02mm,良品率超99.5%。
三、技术突破:效率与安全的双重保障
1.动态环境自适应
通过闪电连接过程优化(LCPO),算法可在迭代中快速收敛,响应时间低于100ms,使具身智能工业机器人适应产线突发障碍或订单变更。
2.人机协作安全
结合模糊逻辑与力控技术,机器人可在人机混合作业中动态调整路径,实现“遇阻即停、避让优先”,保障操作人员安全。