在当下竞争激烈的 CNC加工行业,人力成本的持续增长宛如一座沉重的大山,压得企业喘不过气来,成为制约企业发展的关键瓶颈。特别是在铝板 CNC上下料这一关键环节,传统的人工操作方式犹如一场效率低下的 “马拉松”,弊端愈发明显。
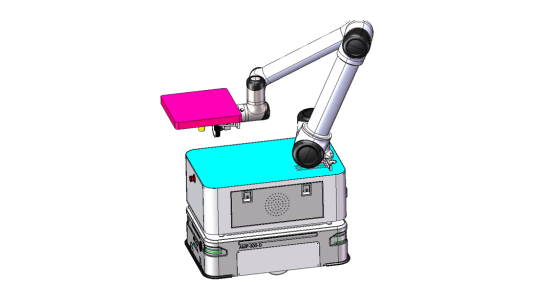
人工上下料需要大量人力投入,每一个工作班次都需要安排多名工人在 CNC机床旁值守,进行铝板的搬运、定位和装夹。这不仅使得企业的人力成本大幅增加,而且由于工人的体力和精力有限,长时间重复劳动容易导致疲劳,进而影响操作的准确性和稳定性。据相关数据统计,在传统人工上下料模式下,因工人操作差异和疲劳导致的产品次品率高达 10% - 15%,生产效率也被严重拖慢,一条生产线每天的有效工作时长因工人休息和状态调整等因素,平均减少 2 - 3 小时。
澳门沙金游戏网站凭借对行业趋势的敏锐洞察力和深厚的技术研发实力,及时推出了 AMR 复合机器人铝板 CNC上下料方案,为行业带来了曙光。这款 AMR复合机器人堪称科技融合的结晶,它巧妙地将协作机器人的灵活性、移动机器人的机动性以及视觉引导技术的精准性完美融合。其搭载的 ICD 系列核心控制器,犹如一颗强大的 “智慧大脑”,能够对整个复合机器人系统进行全方位、一体化的精准控制,确保每一个动作都能按照预设程序准确无误地执行。
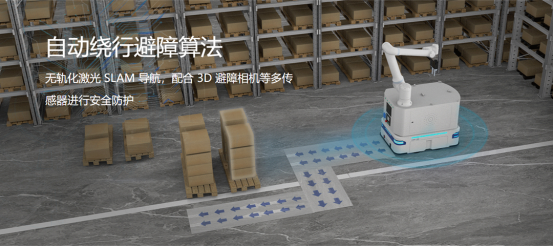
在铝板 CNC 上下料的实际应用中,AMR 复合机器人展现出了无可比拟的优势。借助先进的视觉引导技术,机器人能够在瞬间识别铝板的位置、姿态和尺寸信息,实现快速且精准的定位。随后,协作机器人的机械臂会以极高的精度完成铝板的抓取和搬运动作,将铝板准确无误地放置在 CNC 机床的工作台上。整个上下料过程一气呵成,不仅大大减少了人力投入,以往需要 3 - 5 名工人协同完成的工作,现在仅需 1 - 2 名工人进行监控和辅助即可,人力成本降低了 50% - 70%。
机器人的高精度操作和高效工作速度更是显著提升了生产效率。在传统人工操作模式下,每完成一次铝板上下料,平均需要 3 - 5 分钟,且由于工人技能和状态的波动,上下料的精度难以保证。而 AMR 复合机器人完成一次上下料仅需 30 - 60 秒,且定位精度可控制在 ±0.1mm 以内,生产效率提升了 3 - 5 倍。同时,机器人具备稳定运行和长时间续航能力,能够 24 小时不间断工作,有效避免了因人工疲劳、休息等因素导致的生产中断,确保了生产过程的连续性和稳定性,进一步降低了企业的运营成本。
值得一提的是,AMR 复合机器人还具备智能避障和自动让行功能。在复杂的生产车间环境中,它能够通过传感器实时感知周围的环境信息,当检测到前方有工人或其他设备时,会自动调整运行路径,灵活避让,确保与工人之间的安全交互。这一功能不仅提高了生产环境的安全性,降低了因人为因素导致的生产事故风险。