随着制造业的发展,铝板加工行业对生产效率和产品精度的要求越来越高。然而,传统的CNC加工上下料过程依赖人工操作,不仅效率低下,还容易出现操作误差,影响产品质量。为了应对这些挑战,提高生产自动化水平,复合机器人(AMR)逐渐成为解决方案的焦点。

客户痛点
1.人工操作效率低:CNC加工上下料过程繁琐,需要大量人工操作,导致生产效率低下。
2. 操作误差高:人工上下料过程中容易出现操作误差,影响产品的加工精度和质量。
3. 人力成本高:依赖人工操作不仅增加人力成本,还存在人员流动性带来的管理难题。
4. 安全隐患:人工操作过程中存在一定的安全隐患,可能导致生产事故。
方案目标
本方案的目标是通过复合机器人(AMR)实现生产工艺中“产品搬运”部分的自动化,以提高生产效率和精度。
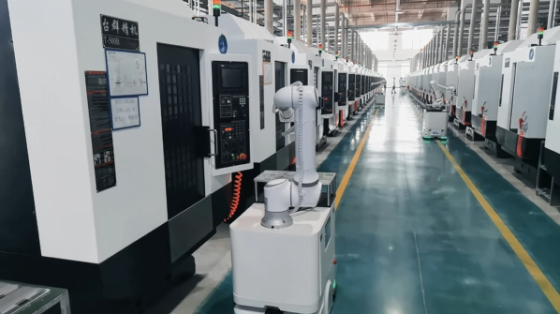
1. 实时调整生产状态:复合机器人AMR根据生产中心的指示,自动完成生产工艺中的产品搬运部分,并能根据生产计划实时调整生产状态。
2. 成品转运:实现复合机器人AMR自动确认CNC加工完成并将成品转运至成品放置区。
3. 上料区物料管理:实现判断上料区物料准备状态,并自动将待加工产品转入空闲或加工完成的CNC设备中。
技术优势
1. 高精度抓取与放置:复合机器人AMR实现抓取误差、放置误差<±1mm,确保加工产品的准确性。
2. 智能避障与安全停机:复合机器人AMR在会车时实现自动让行,有行人或障碍物时自动停止,确保生产安全。
3. 自动对接CNC设备:复合机器人AMR可与CNC设备对接,实现上下料时仓门自动开关,简化操作流程。
4. 高成功率:复合机器人AMR综合抓取放置成功率>99%,显著提高了生产效率和产品质量。
核心价值
1. 提升生产效率:通过自动化上下料和摆盘,减少人工干预,提高生产效率。
2. 提高产品精度:高精度抓取与放置,确保加工产品的质量和一致性。
3. 降低人力成本:减少对人工操作的依赖,降低人力成本,提高生产管理效率。
4. 确保生产安全:智能避障与安全停机功能,减少生产过程中的安全隐患。
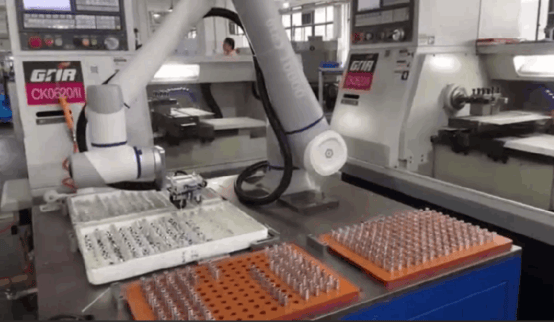
本方案通过引入复合机器人(AMR)实现了CNC加工上下料过程的自动化,显著提高了生产效率和产品精度。复合机器人AMR具备高精度抓取与放置、智能避障、安全停机、自动对接CNC设备等技术优势,能够根据生产中心的指示,灵活调整生产状态,确保整个生产过程的高效、稳定和安全。通过此方案,企业不仅能够提升生产效率和产品质量,还能降低人力成本,确保生产过程的安全性,最终实现智能制造的目标。