随着工业自动化的快速发展,传统的仓库管理模式已难以满足高效、精准的生产需求。特别是在大型生产车间中,人工搬运不仅效率低下,而且容易出错,影响生产进度。针对这一问题,我们提出了基于复合机器人AMR(自主移动机器人)与搬运机器人AGV(自动导引车)的仓库搬运解决方案。
客户痛点
人工搬运效率低下,影响生产进度。
人工搬运容易出错,导致物料混淆或丢失。
现有仓库管理系统缺乏智能化、自动化支持。
解决方案
1、系统架构
我们的解决方案采用了复合机器人AMR与搬运机器人AGV的组合,配合视觉识别系统和FRDS智能调度系统,实现仓库内物料的自动搬运和管理。
2、AMR机器人功能
完成基本的库位管理功能,如物料入库、出库、盘点等。
根据简单指令快速、精准找到物料的位置,并自动完成搬运任务。
整体安全、高效、可靠地完成指令,降低人工干预需求。
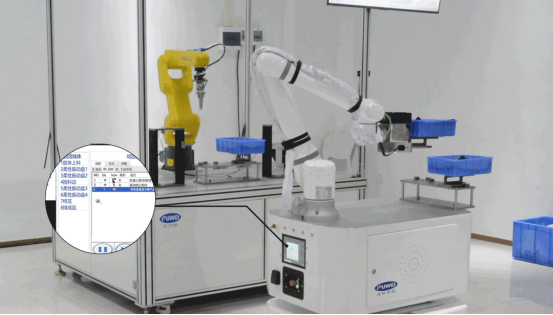
3、AGV机器人功能
负责将AMR机器人转运的料箱运输到指定位置,如生产线、立体库等。
具备电梯乘坐功能,能够自动触发电梯请求并完成层间移动。
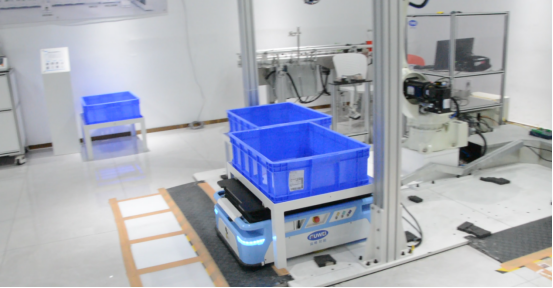
4、视觉识别系统
负责扫码确认料箱信息与料箱在库位的精定位。
配合电动夹爪对料框进行抓取,确保搬运过程中的稳定性。
5、FMS调度系统
对AMR的电量进行检测,低电量时报警或自动充电。
基于AMR车辆管理、交通状态和运输任务指令实现高效的运输流优化。
可与立体库管理系统进行对接,实现自动出入库。
接口丰富,可对接各种物料管理系统、仓储管理系统以及现场传感器信号。
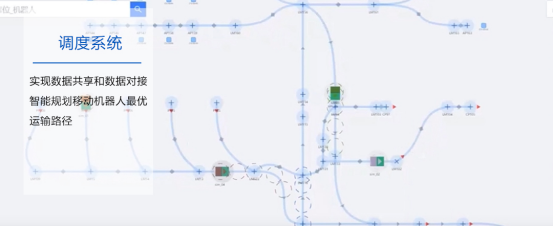
技术优势
1、高效性:通过AMR和AGV的协同工作,大幅提高了仓库内物料的搬运效率。
2、精准性:视觉识别系统确保了物料搬运的精准度,降低了出错率。
3、智能化:FMS调度系统实现了对AMR和AGV的智能调度和管理,提高了系统的自动化水平。
4、灵活性:系统具备高度的可扩展性和可定制性,能够满足不同客户的实际需求。
核心价值
1、提升生产效率:通过自动化搬运系统,降低了人工搬运的劳动强度和时间成本,提高了生产效率。
2、降低出错率:系统的高精准性和智能化管理有效降低了物料搬运过程中的出错率。
3、优化仓储管理:通过与仓储管理系统的对接,实现了对仓库内物料的实时监控和高效管理。
4、提升企业竞争力:通过提高生产效率和降低出错率,有助于提升企业的整体竞争力和市场地位。